Heaterless Vapourizer- The Energy Saviour
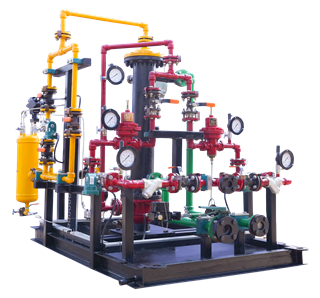
LPG, a clean, efficient, and versatile fuel source, has gained significant importance across industries. LPG is inherently stored as a liquid; however, most appliances utilise it in its gaseous form. Vaporizers bridge this gap by applying heat and converting the liquid LPG into usable gas. Here are two main LPG vaporiser types:
Heated Vaporisers: These are the traditional vaporisers, using electricity, water baths, or steam to heat the LPG and facilitate vaporisation.
Heater less Vaporisers: These innovative devices utilise the principles of thermodynamics to achieve vaporisation without any external heat source.
Heaterless Vapouriser Working Principle
Heaterless Vaporizers, also known as ambient air vaporisers, stand out for their innovative operation principle and eco-friendly profile. LPG from the cylinder manifold system enters a flashing valve. This valve rapidly reduces the pressure of the liquid, causing a drop in temperature due to a phenomenon called adiabatic expansion.
The depressurised and cooled LPG then passes through a shell-and-tube heat exchanger. This exchanger uses ambient-temperature air or water (usually above 15°C) to further vaporise the LPG through heat transfer. Heavier hydrocarbon components with higher boiling points settle down in a liquid trap within the vaporiser and vapour is then released for utility.
Why choose Heater less Vapouriser over traditional Vapouriser
Check out the comparison table highlighting the key differences between heaterless vaporisers and traditional vaporisers for industrial applications.
Factor | Heater less Vapouriser | Traditional Vapouriser |
Operational Cost | HLVs use ambient air to vaporize fluids, adding no extra energy cost; this is especially beneficial in India where energy conservation is critical due to high demand and occasional shortages. | Traditional Vapourisers use electricity or gas, which can be costly. The industrial electricity tariffs in India can exceed, affecting operational costs negatively. |
Maintenance and Longevity | Typically requires less maintenance due to fewer moving parts and no combustion residues or scaling from water, potentially extending its lifespan. | Requires more frequent maintenance to manage wear and tear on heating elements, controls, and to clean combustion by-products. This can reduce the lifespan and increase overall maintenance costs. |
Carbon Footprint | Zero direct emissions as no fossil fuels are burned and no electricity is used, making it a green solution. | Higher carbon footprint due to consumption of electricity or burning of fossil fuels. The emissions depend on the energy source but can significantly contribute to greenhouse gas emissions |
Safety | Higher safety due to the absence of combustion or electric heating elements, reducing risks of fire or electrical hazards. | Increased safety risks associated with the combustion of fuels or electrical faults. |
Flexibility | Highly flexible and can be installed in remote or off-grid locations. | May require proximity to energy supplies (electricity, natural gas lines). |
Heater less vapouriser offers a blend of safety, cost-effectiveness, and eco-friendly efficient energy solution not only represents the significant developmental advancement in LPG industry but also is a greener alternative in industrial operations.
It is also important to comply to IS guidelines and safety protocols while during installation. While talking about safety standards who does that better than SUPERGAS.
Contact us to discuss your industrial energy needs today 9121177930 or drop a mail at industrialsupport@supergas.com